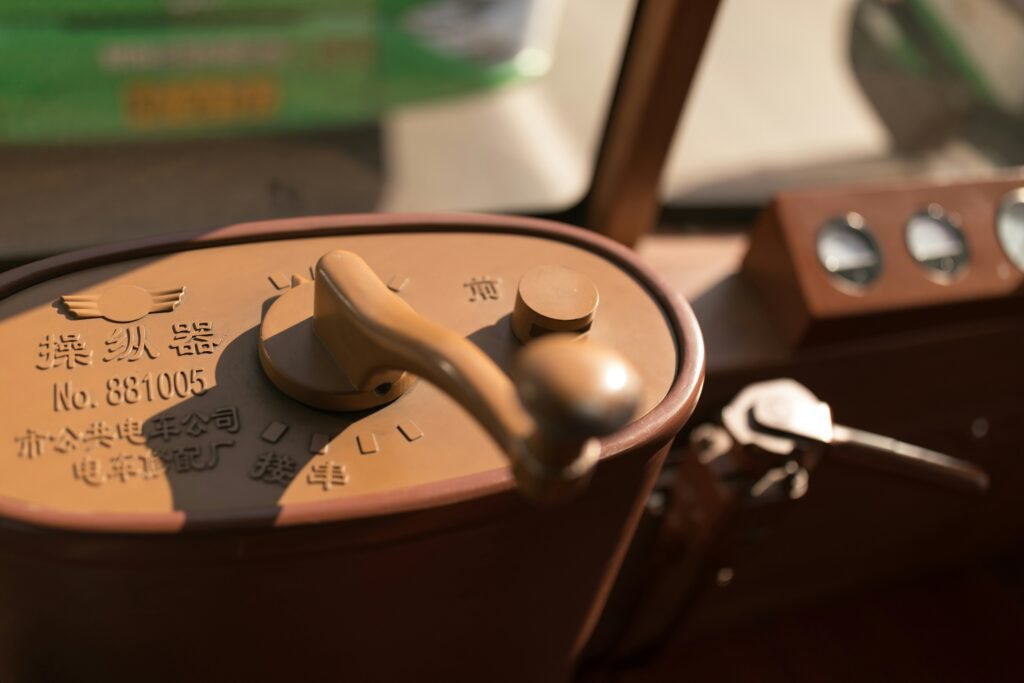
Introduction to FANUC Handwheels
FANUC handwheels are essential devices utilized in the realm of Computer Numerical Control (CNC) machining, serving as manual controllers that facilitate the navigation and operation of CNC machines. These handwheels function by providing operators with a tactile interface to control the movement of machine components with precision and accuracy. The design of FANUC handwheels typically includes a robust wheel, often accompanied by various buttons and switches that enable a seamless user experience.
The primary purpose of FANUC handwheels lies in their ability to grant operators fine control over machining processes. By integrating these handwheels into CNC systems, users can make precise adjustments to the positioning of tools and workpieces, ensuring the highest levels of accuracy in machining operations. This level of precision is particularly beneficial during setup procedures, where manual positioning is crucial for successful machining outcomes.
FANUC handwheels comprise fundamental components including the wheel itself, which allows for smooth rotation, as well as encoders that translate the physical movements of the handwheel into digital signals for the CNC machine. This feedback mechanism is vital for translating manual inputs into machine movements, thereby enhancing overall operational effectiveness. Additionally, many models feature an ergonomic design, ensuring comfortable use during extended periods of operation.
Another significant advantage of utilizing FANUC handwheels is their contribution to improved operator control. The integration of a handwheel into a CNC machine allows for intuitive adjustments, thus reducing the learning curve for operators who may be new to CNC technology. As a result, these handwheels not only support existing operators but also assist in training new personnel in efficient machine operation.
In summary, FANUC handwheels are integral to the functionality of CNC machines, enhancing user control, precision, and operational efficiency. Their design and components facilitate effective manual control, making them invaluable tools in modern machining environments.
Key Features of FANUC Handwheels
FANUC handwheels are designed with precision, comfort, and functionality in mind, making them indispensable tools in various manufacturing environments. One of the most notable key features is their ergonomic design, which ensures that users can operate them for extended periods without experiencing discomfort. The carefully crafted shape allows for a secure grip, reducing the risk of fatigue during intensive machining tasks.
Another defining characteristic of FANUC handwheels is their versatile control options. Users can expect to find controls that enable seamless adjustments to spindle speed, axis movements, and other machinery functionalities. This adaptability allows operators to fine-tune machines precisely to meet specific operational requirements, enhancing overall productivity and efficiency.
FANUC offers a variety of models, each tailored to different applications and user preferences. From compact models ideal for small workshops to larger handwheels suited for industrial applications, the breadth of options ensures that there is a suitable handwheel for every task. This extensive selection reflects the company’s commitment to meeting the diverse needs of the manufacturing sector.
The build quality of FANUC handwheels is another highlight, with rugged materials ensuring durability and resistance to wear and tear. This longevity translates into reduced maintenance costs and increased reliability, allowing businesses to utilize these handwheels effectively over extended periods. Additionally, FANUC handwheels are built to be compatible with various software systems, enabling easy integration into existing setups. This capability simplifies the transition for operators and enhances the overall functionality of the equipment.
Advantages of Using FANUC Handwheels
FANUC handwheels are an integral component in the realm of machining operations, offering numerous benefits that can vastly improve productivity and user experience. One of the primary advantages is the significant boost in operator efficiency. By allowing operators to make precise adjustments with minimal effort, FANUC handwheels can streamline machining processes, enabling tasks to be completed more quickly without compromising quality. Operators can efficiently navigate through programming settings, enhancing overall workflow.
Another notable benefit is enhanced precision in programming. The tactile feedback provided by the handwheels allows operators to make minute adjustments with accuracy that is often difficult to achieve using traditional control methods. This precision is crucial, especially in applications that require meticulous calibration of tools and settings for optimal performance. The ability to dial in exact specifications contributes to improved product quality and reduces the likelihood of errors during the machining process.
Ease of manual control is another significant advantage of FANUC handwheels. The design and ergonomics of these devices enable users to manipulate machinery effortlessly, which is particularly beneficial in environments where quick, real-time adjustments are paramount. The intuitive interface allows for a smoother transition between automated and manual modes, giving operators the flexibility to respond to unforeseen challenges that may arise during machining operations.
Moreover, FANUC handwheels facilitate complex operations that demand intricate adjustments. In advanced manufacturing scenarios where versatility and adaptability are key, these devices can significantly contribute to the overall success of production efforts. By integrating FANUC handwheels into operations, not only do organizations gain a technological edge, but they also enhance their ability to meet stringent production standards and specifications, driving better outcomes for both manufacturers and end users.
Comparison of Different Models of FANUC Handwheels
FANUC offers a range of handwheels designed to enhance the operational efficiency of its CNC systems. When comparing different models, several key factors come into play, including specifications, price ranges, compatibility, and target user groups. Understanding these aspects will assist users in selecting the appropriate handwheel for their specific needs.
The FANUC Handwheel Model A, known for its ergonomic design, features a compact build that makes it easily maneuverable. This model is well-suited for milling applications and is typically priced in the mid-range, appealing to small to medium-sized enterprises. Its compatibility with various FANUC CNC models, such as the Robodrill and Series 0, makes it a versatile choice for users who require reliable performance without the need for advanced features.
In contrast, the FANUC Handwheel Model B offers advanced functionalities, including programmable buttons and enhanced feedback mechanisms. This model is priced higher, making it suitable for larger manufacturing setups that require more control and precision. Compatibility with advanced FANUC systems, such as the Series 30 and the new series of robot controllers, allows for integration into systems demanding superior performance. Typically, users who prioritize automation and efficiency would lean towards this model.
Lastly, the FANUC Handwheel Model C provides a balanced option, incorporating both standard and advanced features. It comes at a competitive price point, attracting a diverse user base, from hobbyists to industrial professionals. Its compatibility with a wide range of CNC systems further enhances its appeal, allowing for seamless upgrades on existing machines.
When choosing among these FANUC handwheels, users should consider not only the price and features but also how well the model aligns with their specific CNC requirements and operational goals. This detailed comparison will help potential buyers make informed choices while navigating the various options available in the FANUC handwheel lineup.
Applications of FANUC Handwheels in Various Industries
FANUC handwheels play a crucial role in numerous industries due to their versatility and precision in controlling machinery. One prominent sector benefiting from these handwheels is the aerospace industry, where precision is paramount. In aerospace manufacturing, FANUC handwheels facilitate high-accuracy movements when assembling complex components of aircraft, such as wings and fuselages. The ability to make fine adjustments enhances operational accuracy, considerably reducing the risk of errors and improving safety outcomes.
Similarly, the automotive industry utilizes FANUC handwheels for both assembly and maintenance operations. In automotive assembly lines, these handwheels are employed for tasks such as aligning components and adjusting tooling setups. With the continuous push for automation, robotics in automotive manufacturing increasingly incorporates FANUC technology, where the handwheels provide operators with manual control capabilities when necessary. This combination of automated precision and manual intervention ensures efficient assembly processes in car manufacturing.
The manufacturing sector more broadly also reaps significant benefits from the integration of FANUC handwheels. In machine shops, for instance, these handwheels assist operators in manual machining processes, allowing for detailed adjustments needed for high-quality outputs. Workshop operators often favor FANUC handwheels for their ergonomic design, which reduces fatigue during extended operations. Applications extend to CNC milling machines, lathes, and other equipment, enhancing the efficiency of production lines.
Real-world examples underscore the versatility of FANUC handwheels across these diverse sectors. Aerospace manufacturers, automotive assembly plants, and machine shops have implemented these tools to streamline processes, enhance precision, and facilitate easy adjustments. Such applications illustrate how FANUC handwheels have become integral in supporting various operational needs in different industries, ultimately contributing to improved productivity and effectiveness in their operations.
User Tips for Maximizing the Use of FANUC Handwheels
FANUC handwheels are vital tools that enhance the precision and efficiency of machine operation. To fully maximize their potential, operators should adopt specific best practices in the operation and maintenance of these devices. One of the primary tips is to ensure regular maintenance of the handwheels, which includes cleaning and inspecting the unit for any signs of wear or malfunction. Regular maintenance not only prolongs the lifespan of the handwheels but also ensures optimal performance during operation.
Operators should also be aware of common mistakes that can significantly affect the effectiveness of FANUC handwheels. For instance, using excessive force when turning the handwheel can lead to damage over time. Instead, a gentle yet firm approach should be utilized, allowing for more accurate and controlled movements. Another common mistake involves failing to properly set the handwheel mode, which can lead to unexpected results. Ensuring that the correct mode is selected prior to operation is crucial for achieving the desired outcomes.
To master the control offered by FANUC handwheels, operators can employ techniques that enhance their interaction with the machinery. Developing a rhythm while using the handwheel can lead to smoother operation. Practicing different speeds and pressure levels can help operators find the most effective way to manipulate the handwheel for various tasks. Utilizing both the handwheel and the machine’s programmed features together can also optimize workflows and enhance productivity.
Moreover, continuous education on the latest functionalities and updates related to FANUC handwheels can provide operators with additional insights and techniques that will elevate their operational skills. Engaging with community forums or participating in training sessions can be beneficial in this regard. By implementing these best practices and continually refining their skills, operators can significantly improve machine performance and ensure efficient use of FANUC handwheels.
Troubleshooting Common Issues with FANUC Handwheels
FANUC handwheels are essential tools utilized in various industrial applications, allowing operators to control machinery with precision. However, like any equipment, they may encounter issues that require troubleshooting to maintain optimal performance. Identifying and resolving problems effectively ensures continued operational efficiency.
One of the most frequent problems users may experience is unresponsiveness from the handwheel. If the handwheel does not respond as expected, the first step is to verify the connection to the control system. Inspect the cabling and connectors for any signs of damage or disconnection. Re-establishing a secure connection often resolves this issue. Additionally, it’s essential to check the power supply to ensure that the handwheel is receiving adequate voltage.
Error messages frequently appear on the control interface when malfunctions occur. Common messages include “Handwheel Not Found” or “Communication Error.” Upon encountering such errors, consult the FANUC manual for specific troubleshooting guidelines tailored to your model. Often, these messages indicate issues with configuration settings or communication protocols that need adjustment. Restarting the control system can sometimes clear transient errors; if persistent, further diagnostics may be required.
Another common issue is the handwheel’s calibration. If movements are not accurately reflected on the display, recalibrating the handwheel may solve the problem. Most FANUC models include a calibration option in their settings menu, which guides users through the process of aligning the handwheel’s physical movement with the corresponding control data.
In some cases, wear and tear can cause mechanical issues. Regular maintenance, including cleaning and inspecting the handwheel’s internal components, is crucial to prevent malfunctions. Replacement of worn parts should be done promptly to maintain performance. Monitoring the handwheel’s functioning and addressing minor issues before they escalate is vital for optimal operation.
Future Trends in Handwheel Technology
The landscape of handwheel technology, particularly in the context of FANUC systems, is poised for transformative advancements that integrate modern technology to enhance usability, precision, and efficiency in CNC machining. One of the most promising trends is the incorporation of artificial intelligence (AI) into handwheel systems. AI contributes to more intuitive user experiences by adapting the interface based on user behavior and preferences. This personalization can potentially lead to more efficient operation, as machines recognize patterns and streamline workflows accordingly.
Another significant progression is the rise of touchscreen interfaces that facilitate advanced controls across CNC machinery. Touchscreen technology allows for a more dynamic interaction between operators and machines, supplementing traditional handwheels with enhanced visual feedback, graphical representations, and multi-touch capabilities. Moreover, touchscreens can minimize the learning curve for new users, making CNC machines more accessible and easier to operate. These interfaces can also display real-time data, providing operators with critical information that informs decision-making during the machining process.
Further innovations in user interfaces extend beyond touchscreens, as voice-activated commands and gesture controls are being explored to make CNC machines even more user-friendly. This would eliminate the need for physical contact with handwheels, promoting a cleaner environment and reducing wear and tear on equipment. Additionally, advancements in haptic feedback technology could enhance user interaction, allowing operators to feel the resistance and precision during operations without relying solely on visual feedback.
As FANUC handwheel technology evolves, the aim remains to foster efficiency and accuracy in CNC processes. The integration of AI, touchscreens, and innovative user interfaces not only promises to improve the operator experience but also ensures that future machines are equipped to meet the demands of modern manufacturing.
Conclusion
FANUC handwheels play a significant role in the efficient operation of modern machining processes, particularly in computer numerical control (CNC) environments. Throughout this guide, we have explored several key features and benefits of these handwheels, establishing their importance in enhancing user experience and operational precision. These devices are designed to provide operators with not only fluid control over machine axes but also an intuitive way to navigate complex programming tasks typically associated with CNC machinery.
One of the primary advantages of FANUC handwheels is their ergonomic design, which facilitates prolonged use without causing operator fatigue. Additionally, the tactile feedback provided by these devices ensures a high level of accuracy, allowing machinists to achieve precise movements and adjustments in their work. As a result, the integration of FANUC handwheels contributes significantly to the overall productivity and efficiency of machining operations, making them an invaluable tool for both novice and experienced machinists.
Moreover, the adaptability of FANUC handwheels across various machining applications underscores their versatility. Whether employed on lathes, milling machines, or other CNC equipment, they can effectively enhance the control experience. This versatility also allows operators to customize their workflows, which can lead to increased job satisfaction and improved output quality. Recognizing their utility, many manufacturers are increasingly incorporating FANUC handwheels into their CNC systems to optimize performance.
In conclusion, FANUC handwheels are essential tools that facilitate a smoother and more effective CNC machining experience. Their integration into modern manufacturing processes not only enhances operator skill but also contributes to increased operational efficiency. As the demand for precision and productivity continues to grow in the manufacturing sector, considering the adoption of FANUC handwheels in your own machining applications may serve as a strategic advantage.